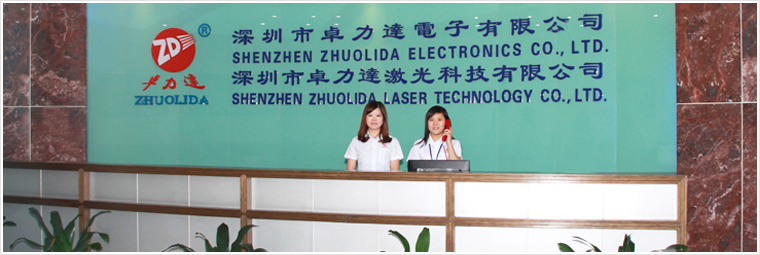

金属蚀刻的定义
金属蚀刻定义:蚀刻(etching)也称金属腐蚀,或光化学蚀刻.是将金属材料使用光化学反应的移除的技术,是冲压工艺的延伸,是蚀刻更专业化的体现.
蚀刻的原理: 指通过曝光显影工序、将产品的图形转移到金属钢片上,将要蚀刻区域的保护,不要的区域除去保护膜裸露出金属部分,再用化学药水溶液起到腐蚀的作用,形成凹凸半刻或者镂空成型的效果。卓力达经过不断改良和工艺设备发展,目前用于航空、机械、化学工业中电子薄片零件精密蚀刻产品的加工,特别在半导体制程上,蚀刻更是不可或缺的技术
金属蚀刻, 就是只做金属的蚀刻, 不锈钢,铜合金, 铝合金,钛合金及钼材, 都可以用蚀刻的工艺加工成型, 特别是精度要求高的产品, 蚀刻工艺是首选 ! 不锈钢有多种牌号,常用的有 SUS304, SUS301, SUS316, SUS631等 。不锈钢蚀刻工艺的难点在于:不锈钢本身的搞腐蚀性能较强,如何保证不锈钢蚀刻工艺加工完成后的产品的尺寸,精度,表面都能完全符合客户的要求。这就需要在不锈钢蚀刻工艺蚀刻管控的过程中,设备,人员,技术相配合,有较好的加工设备,有过硬的技术水平。
金属蚀刻工艺的流程详解
金属的种类不同,其蚀刻的工艺流程也不同,但大致的工序如下:金属蚀刻板→除油→水洗→浸蚀→水洗→干燥→丝网印刷→千燥→水浸2~3min→蚀刻图案文字→水洗→除墨→水洗→酸洗→水洗→电解抛光→水洗→染色或电镀→水洗→热水洗→干燥→软布抛(擦光)光→喷涂透明漆→干燥→检验→成品包装。
1.蚀刻前处理:在金属蚀刻之前的工序都是前处理,它是保证丝印油墨与金属面具有良好附着力的关键工序,因此必须要彻底清除金属蚀刻表面的油污及氧化膜。除油应根据工件的油污情况定出方案,最好在丝印前进行电解除油,保证除油的效果。除氧化膜也要根据金属的种类及膜厚的情况选用最好的浸蚀液,保证表面清洗干净。在丝网印刷前要干燥,如果有水分,也会影响油墨的附着力,。
2.附膜(干膜或湿膜):钢片清洗干净后,在表面滚涂感光油墨或直接贴干膜,(以便制得较厚的丝网模版,这样才使得遮盖性能好,蚀刻出的图纹清晰度高)丝网版的胶膜在光的作用下,产生光化学反应,使得光照部分交联成不溶于水的胶膜,而未被光照部分被水溶解而露出丝网空格,从而在涂有胶膜丝网版上光刻出符合黑白正阳片图案的漏网图纹。把带有图纹的丝印网版固定在丝网印刷机上,采用碱溶性耐酸油墨,在金属板上印制出所需要的图纹,经干燥后即可进行蚀刻。
3.金属蚀刻后处理:金属蚀刻后必须除去丝印油墨。一般的耐酸油墨易溶于碱中。将蚀刻板浸入40~60g/L的氢氧化钠溶液中,温度50~80℃,浸渍数分钟即可退去油墨。退除后,如果要求光亮度高,可进行抛光,然后进行染色,染色后为了防止变色及增加耐磨、耐蚀性,可以喷涂透明光漆。对于一些金属本身是耐蚀性能好而且不染色的,也可以不涂透明漆,要根据实际需要而定。
(二)金属蚀刻化学蚀刻溶液配方及工艺条件
蚀刻不同的金属要采用不同的溶液配方及工艺条件,常用金属材料的蚀刻溶液配方及工艺条件见表6—4~表6-6。
(三)工艺操作条件的影响
蚀刻是金属板模图纹装饰过程中的关键,要想得到条纹清晰、装饰性很强的图纹制品,必须注意控制好蚀刻工艺的条件。主要是蚀刻溶液的温度和蚀刻时间。溶液温度稍高,可以提高金属溶解的速度,也就是蚀刻的速度,缩短蚀刻所需要的时间,但是蚀刻溶液一般都是强酸液,强酸液在温度高的情况下腐蚀性强,容易使防护的涂层或耐蚀油墨软化甚至溶解,使金属非蚀刻部位的耐蚀层附着力下降,导致在蚀刻和非蚀刻交界处的耐蚀涂层脱落或溶化,使蚀刻图纹模糊走样,影响图纹的美观真实和装饰效果,因此温度不宜超过45℃。同样,如果蚀刻的时间太长,特别是蚀刻液温度较高的情况下,耐蚀油墨或防护涂层浸渍时间过长,也同样起到上述的副作用和不良后果,因此时间控制上也要适当,不能浸得太久,一般不宜超过20~25min。
(四)化学蚀刻图纹装饰实例
?1.装饰用的材料:装饰用的金属板材:普通钢材、不锈钢、铜及铜合金、铝及铝合金等,以不锈钢板为例说明,板厚l~3mm。化工原料:丝印感光胶(例如浙江昆山市化工涂料厂生产的DH重氮型),耐酸油墨有99-956型和99-200K型等一(广东顺德大良油墨厂产品),其他为常用化学化工药品。
2.工艺流程:不锈钢板→除油→水洗→干燥→丝网印刷→干燥→水浸→蚀刻图纹叶(片)水洗→除墨→水洗→抛光→水洗→着色→水洗叶(片)硬化处理→封闭处理→清洗叶(片)干燥→检验→产品。?
3.具体操作及注意事项:
(1)除油 ?除油是为了使丝印油墨与板材有良好的附着力,所以金属板在印前必须彻底把油除干净。除油的方法很多,可以根据情况及需要选择,例如采用常规的化学除油、表面活性剂除油,甚至电解除油、超声除油等,也可以选用商品的专用除油剂。彻底清洗干净后,经干燥再转入丝网印刷。
(2)丝网印刷选用l50目不锈钢、聚酯或尼龙单丝维网,用绷网机固定在网框上,再用上浆器刮涂DH重氮型感光胶,涂覆2~3次,涂膜干燥后,将拍摄好的图纹黑白胶片附着在涂膜丝网上,经曝光、显影后,即制得丝印模板,然后再将不锈钢板、图纹模板固定在丝网印刷机对应位置上,采用碱溶性的耐酸油墨,印上所需要的图纹,自然干燥(或烘干)。如果烘烤,则温度不宜过高及时间不宜过长,否则油墨的碱溶性降低,到除油墨时,不易清除干净。一般情况下,自然干燥1h。烘干为55~60℃,4~5min。
(3)图纹蚀刻工艺 ?图纹化学蚀刻溶液的配方及工艺条件如下: 氯化铁(FeCl3) 650~800g/L 蚀刻加速剂 85~lO0g/L 盐酸(HCl,38%) 85~120g/L 蚀刻液温度 10~45℃ 磷酸(H3P04) 20~30g/L 浸渍时间 l5~25min
在操作过程中要严格控制溶液的温度和时间。温度过高、时间过长,油墨与板面的附着力下降,在蚀刻与非蚀刻处可能出现油墨的脱落,导致图纹模糊走样,影响蚀刻的精度和装饰效果。
(4)蚀刻后除墨蚀刻后必须除去保护的碱溶性耐酸油墨。方法是浸入40~60g/L NaOH碱液中,温度控制在60~70℃,浸泡3~5min,以除干净油墨为准。然后用水冲表面的碱液至中性。
(5)蚀刻后处理经蚀刻后的图纹不锈钢板经过除油墨及清洗干净后,可以根据用户的不同需要作如下附加装饰处理。 ①对要求保留不锈钢原色及光泽的,经除油墨及清洗干净后,放进50%HN03(体积分数)和50%H20的溶液中浸泡l0~20min,作钝化处理,使不锈钢蚀刻图纹板获得新的保护膜,即可得装饰制品。 ②对要求保留不锈钢原色,但光亮度要求更高、更光亮的,经除油墨及洗净后,先进行电解抛光,然后再表面钝化。电解抛光的溶液配方及工艺条件如下:柠檬酸 50%~70% 溶液温度 40~60℃ 硫酸 20%~l5% 电流密度 15~30A/dm2 水 10%~25% 抛光时间 5~lOmin阴极材料 铅板 ③为了提高制品的装饰性,有些用户要求改变原有不锈钢的颜色。对此,不锈钢经蚀刻图纹及清除干净表面的油墨后,先进行电解抛光,然后化学着色或电解着色,着色后必须对着色膜进行硬化处理及封闭处理,最后得到所需的装饰制品。化学着色溶液的配方及工艺条件如下: 硫酸(H2S04) 270~300g/L 溶液温度 65~80℃ 铬酐(Cr03) 450~500g/L 处理时间 由蓝色→橙色→金黄 (NH4)6Mo7024·4H20 40~50g/L 色一绿色,颜色随时间变化 化学着色后要进行硬化处理(或固膜)以便稳定着色膜,改善着色膜的质量及耐磨性。硬化处理的溶液配方及工艺条件如下: 重铬酸钾(K2Cr207) 10~20g/L 溶液温度 65~80℃氢氧化钠(NaOH) 3~5g/L 处理时间 2~3min溶液pH 6.5~7.5 ? ? ? ?着色膜经上述硬化(固膜)处理后,硬度、耐磨、耐蚀性都已提高,但膜层有孔隙,需要进一步进行封孔处理。如果着色膜本身质量好、硬度高,可以不必进行硬化处理,但必须进行封孔处理。封孔处理液的成分及工艺条件如下:硅酸钠(Na2Si03) 10g/L 溶液温度l00℃ 沸腾十二烷基苯磺酸钠 2~5g/L 处理时间 4~6m 除了化学着色外,也可以用电解法着色,电解着色溶液的配方及工艺条件如下:
铬酐(Cr03) ?80~260g/L 电流密度 0.05~0.10A/dm2 硫酸(H2S04)25%(体积分数) 着色时间l0~30min 溶液温度 70~90℃ 本着色溶液在着色过程中,工艺条件对颜色有较大影响。首先是硫酸对铬酐的浓度比例对颜色的影响,铬酐浓度高时,为金黄色,浓度再高,则变成紫红色。温度对着色的影响为:温度升高,色泽逐渐加深。着色时间的影响为:5min便开始着色,随着时间的增加,颜色加深,20min后色泽基本稳定。电流密度对着色的影响为:0.03A/dm2时,为玫瑰色,0.05A/din2时,则为l8K金色。电解着色后同样需要进行硬化处理,硬化处理可以用化学法(上述举例),也可以用电解法。电解法硬化处理的溶液配方及工艺条件如下: 铬酐(Cr03) 240~280g/L 阴极电流密度 0.2~1.0A/dm2 硫酸(H2S04) 2~3g/L 阳极材料 铅或铅锑合金 溶液温度 50~55℃ 处理时间 10~15min
硬化处理后,同样要进行封闭,在 沸 腾 的 硅 酸 钠 溶 液 中 煮 5min, 取出清洗、 干燥, 便可得到各种色泽的图纹装饰板
蚀刻工艺的发展
蚀刻技术的起源从有记载的数据可以追溯到14世纪,在那时人们对金属蚀刻还只能说是一种加工技术,还不能上升到工艺这个范畴,因为在当时及以后的几百年里,蚀刻只是由加工者自己的技术水准来决定其加工质量,而不是所有人都可以学到这门技术。到了17世纪,由于硫酸、盐酸、氢氟酸、硝酸、苛性碱等强有力地具有蚀刻作用的强酸、强碱被先后发明,才使蚀刻技术有了新的发展。
17世纪后期,人们已经开始使用蚀刻技术进行测量工具刻度的加工,作为工具已有别于以前的艺术品的加工,它要求其产品的一致性高,这就要求蚀刻技术能做到一定批量的产品在质量上的一致性,这就需要一种规范来精确规定每个加工工序的要求。
到了20世纪,由于与金属蚀刻有关的技术先后得到了解决,同时金属蚀刻技术经过几百年的的艰难历程,人们也积累了足够的经验,并在这些经验之上形成了蚀刻的理论。使蚀刻加工从航空航天到普通民用产品都被大量采用。
蚀刻工艺的深度及表面粗糙度控制
经常会有需要半刻的产品, 而且半刻深度公差及表面粗糙度都有要求,
半刻深度靠蚀刻时间和蚀刻机的压力 来控制, 一般来说, 蚀刻时间越长, 半刻深度越深 , 压力越大, 半刻深度越深, 这两点都要管控
表面的粗焅度靠药水浓度控制, 蚀刻速度越慢, 表面越细腻, 蚀刻速度快的, 表面粗糙.
几种金属蚀刻不锈钢材料选择和用途
很多易变的因素表示侵蚀介质的特征,即化学制品和其浓度、大气状态、温度、时间,所以假如不了解介质的准确的性质,要使用材料、选择材料是难题。但是,以下可作为选择指南:
304型 广泛使用的材料。在建筑中能经受一般的锈蚀,可抵挡食物加工介质浸蚀(但含有浓酸和氯化物成分的高温状态可能泛起侵蚀),能抵挡有机化合物、染料和广泛的各种各样的无机化合物。304L型(低碳),耐硝酸性好,并耐用中等温度和浓度的硫酸,广泛地用作液态气体贮罐,用作低温设备(304N)、用具其它消费产品,厨房设备、病院设备、运输工具、废水处理装置。
316型 比304型含有稍多的镍,并含有2%─3%的钼,耐蚀性比304型好,特别是在倾向于引出发点侵蚀的氯化物介质中。316型已发展用作亚硫酸盐纸浆机,由于它耐用硫酸化合物。而且,它的用途已扩大到在加工产业中处理良多化学制品。
317型?含有3%—4%的钼(在这个系列中也是所得到的较高的水平),并含有比316型较多的铬,具有更高的耐点侵蚀和裂痕侵蚀机能。
430型 比304型合金含量低,用作在温顺的大气中高抛光装饰用途,也可用作硝酸和食物加工设备。
410型在三种一般化用途的不锈钢中具有最低的合金含量,需要强度和耐蚀性配合的高承力部件选用,例如坚固件。410型在温顺的大气中、水气中和很多缓和的化学产品介质中耐蚀。
2205型 比304型和316型优胜,由于他对氯化物应力侵蚀裂纹具有高的抵挡力,并具有大约两倍的强度。316不锈钢板、316不锈钢管、316不锈钢带不锈钢的发展,不锈钢的历史
毕业于英国谢菲尔德大学的著名冶金科学家亨利·布雷尔利(Harry Brearley)于20世纪初期发明了不锈钢。 不锈钢的发明和使用,要追溯到第一次世界大战时期。英国科学家布享利·布雷尔利受英国政府军部兵工厂委托,研究武器的改进工作。那时,士兵用的步枪枪膛极易磨损,布雷尔利想发明一种不易磨损的合金钢。布雷尔利发明的不锈钢于1916年取得英国专利权并开始大量生产,至此,从垃圾堆中偶然发现的不锈钢便风靡全球,亨利·布雷尔利也被誉为“不锈钢之父”。
金属蚀刻工艺的特点
1.目标性,所谓目标性就是通过某一工艺流程的全过程有一个明确的输出,或者说要达到某一特定的目的。对金属蚀刻而言,这个目的就是满足其设计图纸对产品的要求。更具体地说,这些要求包括产品的蚀刻尺寸要求、经蚀刻后的表面粗糙度要求等。
2.内在性,所谓内在性,是指一个工艺流程必须需要有其内在的特定内容,也可以说是内容的实在性。这些内容包含于工艺流程的每一个步骤中,以及参与这些步骤的所有操作者的行为过程。
3.整体性,所谓整体性,是指工艺流程至少要有两个或两个以上的工序组成。因为,作为流程而言的工艺流程不可能是由一个加工步骤来完成,同时一个加工步骤也无法在工艺流程中完成流转,至少要两个或两个以上的步骤及其相关活动才能建立起一个基本的结构或者关系,才能进行流转。对于金属蚀刻工艺流程而言,也是由多个工序、各工序的工艺参数、各工序规定的工具及其相关设备组合而成的一个完整的工艺规范统一体,并且相互之间是不可分割的。
金属蚀刻的曝光原理
首先将需蚀刻的图形通过光绘的方式转移至两张完全一致的胶片菲林上,或是通过光刻的方式转移至两张完全一致的玻璃菲林上。然后通过人工对位方式或机器对位方式将菲林对准。再将已涂布感光油墨或贴好感光干膜的钢片置于菲林中间,吸气后即可曝光。曝光时对应菲林黑色处的钢片未被感光,对应菲林白色处的钢片感光,钢片感光处的油墨或干膜发生聚合反应。最后经过显影机,钢片上被感光的油墨或干膜不被显影液溶化,而未感光的油墨或干膜在显影液被溶化去除,这样需蚀刻的图形通过曝光就转移到钢片上去了。
曝光是在紫外光照射下,光引发剂吸收光能分解成游离基,游离基再引发不聚合单体进行聚合交联反应,反应后形成不溶于稀碱溶液的体形大分子结构。曝光一般在自动面曝光机内进行,现在的曝光机根据光源的冷却方式不同分风冷和水冷两种。曝光成像质量除干膜光致抗蚀剂的性能外,光源的选择,曝光的时间(曝光量)的控制,照相底版的质量等都是影响曝光成像质量的重要因素。
当曝光不足时,由于单体聚合不彻底,在显影过程中,胶膜溶涨变软,线条不清晰,色泽暗淡,甚至脱胶,在蚀刻过程中膜起翘,渗镀,甚至脱落;当曝光过度时,会造成难于显影,胶膜发脆,留下残胶等弊病。曝光将产生图像线宽的偏差,过量的曝光会使图形线条变细,使产品的线条变粗。根据显影后干膜的光亮程度,图像是否清晰,图像线宽是否与原底片相符等来确定适当的曝光时间。
蚀刻加工前的滚涂保护油原理
使胶辊与钢轮平行靠紧,并匀速向内旋转,油墨从胶管喷至钢轮上,均匀调节胶辊与钢辊之间的紧密度,就可以控制粘附在胶辊上的油墨厚度与均匀度;钢片由输送带往前匀速推进,与胶辊适当接触,胶辊上的油墨就均匀的转印到钢片表面上。 在蚀刻的防蚀层制作中涂装技术应用较多,常用的涂装方法有丝印法、浸涂法、喷涂法、电泳涂装等。涂覆的防蚀层表面应均匀完整、无砂眼、白点等,如发现防蚀层有上述质量缺陷,且这些缺陷又在图文线条附近,特别是精细图文线条,应退除防蚀层重新涂覆。工件上喷涂的感光油墨干燥后,在进行曝光之前要进行质量检查。检查项目包括油墨表面无划伤、气孔,油墨的均滚涂匀性等,如达不到这个要求应将整个板面的油墨退掉重新滚涂。
*光阻与钢片的附着力是靠光阻膜顺着钢片表面流动达成。
*加热可降低光阻的粘度并增加流动性,压力可将流动状态的光阻挤入钢片表面。
贴膜时,先从膜上剥下聚乙烯薄膜,然后在加热加压的条件下将干致抗蚀层粘贴在不锈钢材料上面。干膜中的光致抗蚀层受热后变软,流动性增加,借助于热压辊的压力和光致抗蚀层中胶黏剂的作用完成贴膜过程。干膜光致抗蚀剂是20世纪70年初期发展起来的一种感光材料,至今已有多种产品用于要求不同的生产需要。干膜具有良好的工艺性能,优良的成像性和耐化学药品性能,在线路板制造、图文制作及精密零件的切割上都得到了非常广泛的应用。
蚀刻加工速度和侧蚀量
在蚀刻加工中两个最关键同时也是最为重要的参数。蚀刻速度决定了蚀刻加工周期的长短,蚀刻速度越快,蚀刻加工周期越短,生产效率越高,反之生产效率较低。但是,蚀刻速度也并非越快越好:1蚀刻速度越快,在单位时间内对金属的蚀刻量就越大,产热量增大,腐蚀液温度变化快,不利于蚀刻速度的恒定;2、蚀刻速度太快,对于深度要求很精准的零件加工不易控制;3、蚀刻速度越快,经蚀刻后的金属表面质量越低,明显影响蚀刻表面的平滑度和光泽度;4、高的蚀刻速度往往都需要高浓度的腐蚀剂浓度、高腐蚀性的化学试剂、高的蚀刻温度等。这些因素一则使腐蚀剂成本增高,同时对抗蚀层的要求增高,成本增加。再则,高浓度的腐蚀剂和高的蚀刻温度都会增加对环境的污染和对操作人员的危害。在实际应用中,对于那些蚀刻量较大的零件,可以采用“先快后慢”的方法进行。所谓“先快后慢”就是先用蚀刻速度较快的腐蚀液进行一次蚀刻,当蚀刻深度接近设计要求值后,再换用蚀刻速度较慢的腐蚀液进行精度蚀刻,这样做虽然增加了工序,但缩短了加工时间,同时又保证了蚀刻精度和表面光泽度。至于快速蚀刻时间的确定,需要根据零件加工要求而定,一般可以选择总蚀刻量的80%-90%为宜。
在金属蚀刻加工的材料中,以铜的侧蚀最小。一般铜材质分为不同的牌号,以对应生产不同的产品。下表为您清楚的了解国内外不同铜牌号的对应表,以方便朋友们选择相应牌号的材料进行加工产品。
蚀刻加工时间的计算
在蚀刻工艺方法中,是把零件或已做过图文防蚀层的零件置放于腐蚀液中进行蚀刻,并一直蚀刻到金属厚度达到要求的或图文深度达到要求为止。在整个蚀刻过程中,存在三个可变因素,即:蚀刻深度、蚀刻速度和蚀刻时间。这三者的关系式如下:
V=h/t
式中:V为蚀刻的速度(mm/min),这里所指的化学蚀刻速度是指单面的蚀刻速度;h为蚀刻深圳(mm);t为蚀刻时间(min)
此式为计算蚀刻深度和蚀刻速度的基本公式。对于整体蚀刻或成型的化学蚀刻加工及镂空图文的蚀刻往往都是两个面同时进行。这种双面蚀刻加工的速度比只在一个面进行的蚀刻加工的速度快1倍,在金属材料一定的情况下,影响蚀刻加工速度的因素很多,其中最主要的是蚀刻剂的种类、浓度及蚀刻温度。如果蚀刻剂的浓度及蚀刻条件一定,材料的特性及热处理状态对蚀刻加工的速度同样有很大的影响。
金属蚀刻 材料SUS304 SUS301 不同状态下的机械性能
金属蚀刻 板厚-硬度值 测量负荷表
要做好金属蚀刻,必须了解材料的性能,我们知道不锈钢材料有1/2H, 3/4H , FH EH,等等, 硬度范围 HV100-600以上,比如304-FH在硬度 HV370以上,但如果厚度不同, 硬度测量负荷是一样吗? 答案是:不一样,具体测量规则见下表; 板厚与硬度值测量负荷表,参大家查阅!
金属化学蚀刻最主要的限制与难点
金属蚀刻加工虽然具有诸多优点,它对于某些用机械方法难于加工的场合确实有独到之处。但是蚀刻加工也不是一种万能的加工方法,它也会受到很多因素的限制。只有真正认识到蚀刻在某些方面的限制与困难,才不至于把这种工艺方法运用到一些不适合于蚀刻加工或者运用起来困难很大的用途上去。
局限1 , 蚀刻工艺有连接点 : 产品的外形边缘会产生内凹或外凸的连接位, 如果是外观件, 需要用其他加工方法去除,
局限2, 半刻内侧存在R角, 不是垂直的,R角的大小随着厚度不同, 大小不同, 当半刻槽需要组装零件时,中间产生间隙.
蚀刻只能以零件原有表面状态为基础,累计进行切削。因此经过蚀刻加工后的零件形状及表面状态,与零件原始的形状与表面状态有直接关系。更多的情况是经蚀刻后的加工表面完全与原来的初始基准表面状态保持平行。而形成蚀刻边缘的几何形状,又主要与材料厚度有关。从这些限制可以看出,蚀刻不能用于表面粗糙的板材、棒材等来加工形状复杂的零件。如需要在复杂零件上的某些部位加工出很薄的腹板或一些浅的凸缘时,就必须先用机械的方式将全部几何外形加工到一定程度,而接下来的蚀刻只是平行于已加工好的表面把金属均匀地蚀刻去掉一层,以达到所要求的厚度和形状。同时蚀刻无法在所加工的边缘进行垂直侧面的加工,只能加工出一个半径近似于腐蚀深度的圆弧形状如图所示:(b)图所示。 采用一些特殊的腐蚀剂,在控制良好的情况下,可以蚀刻加工出一种斜削边的形状如图(c)所示。
单纯的外形尺寸加工,也就是常说的化学下料,通常只有两种情况才会采用。1、对于材料厚度不大的精巧零件的加工,如种弹簧片或其它精巧结构件的加工;2、驿于那些材料很硬而难于进行机械加工的金属材料进行大尺寸精密下料时的外形加工,这些材料往往是不可能用机械方法进行仿形加工。随着照相化学蚀刻技术的不断完善和普及,用于外形尺寸加工可以做到很高的几何外形保真度和化学蚀刻精度。
金属蚀刻的用途特点
(1)去毛刺。由于不锈钢板在冲制或机械加工后,在端面或棱角处存在毛刺,不仅影响产品的外观,也影响机器的使用效果,如果采用机械抛光或手工去毛刺,不仅工效低,也不能满足设计的圆角倒角要求,采用特殊的化学抛光或电化学抛光溶液,对毛刺进行腐蚀加工,而又不损害表面光洁度,甚至可以提高表面光洁度。这是表面处理与机械加工的结合。
(2)除去多余尺寸。如某不锈钢弹簧钢丝,其线径要求φ0.8~0.84,而实际线径是和0.9,如何使制成品均匀变为φ0.8~0.84,如何有效地去除机加工过程中的毛刺和热处理过程中产生的氧化膜?如要采用机械抛磨和钳修的方法除去毛刺、氧化皮和钢丝直径圆周上均匀地除去0.06~0.1mm.不仅加工工艺性差,效率低,加工质量也难以保证。利用化学抛光的特殊溶液,可以同时达到除去毛刺,氧化皮,均匀除去多余的线径尺寸的目的。又如对某些片状不锈钢零件,尺寸大些,也可以利用电化学抛光的特殊溶液适当减薄厚度尺寸,达到产品尺寸要求。
(3)铣切加工。将不锈钢材料需要加工的部位暴露于化学铣切液中进行铣切加工,从而获得一定形状或尺寸的零件,达到具有立体感、装饰性的目的。利用丝网漏印,可对不锈钢表面化学铣切出文字、花纹、图样,达到一定的深度,再填充上一定的不同的色彩,如奖牌、标牌、铭牌等。
蚀刻工件的后处理问题
蚀刻工件的保护膜去除之后,就显露出光泽的金属本色,例如:黄铜装饰件、铭牌、未蚀刻到的凸处是光亮的金黄色。被蚀刻到的凹处则是亚光或是无光的,层次清晰,经漂洗钝化后,表面罩上保护漆,即为成品。也有在被蚀刻到的凹处填上各种色漆,形成彩色的图案再罩上保护漆。高档工艺品脱膜后往往还要电镀,镀合金或真金或白银,再填漆罩光或直接罩光。也有局部电镀的,例如:不去除保护膜,在被蚀刻的部位镀上其它颜色,然后再去除保护膜,这样就是金银二色的产品了。显得精致、华丽,高贵。罩光的用保护漆以前有人用自干漆,当时好看但不耐久,现在多用烘干型涂料,紫光光(UV)固化涂料或电泳涂料。工业产品中使用不锈钢材质的零件,通常去除保护膜,清洗干净就好了,当然,有特殊要求的也可能需要表面着色,钝化或涂层。
蚀刻加工过程中的环境问题
金属蚀刻加工过程中影响的因素主要是酸、碱和三氯化铁,对其废涂必须妥善处理,不可随便排放。对于酸、碱废水一般都是用中和的方法进行处理,正好在蚀刻加工过程中有碱性废水,也有酸性废水,它们可以相互中和,当然不可能正好酸碱平衡,这就要检测PH值,缺啥补啥,使PH值达到排放的要求,同时还要清除过量的金属离子,经沉淀后,清水方可排放。三氯化铁废液对环境的污染,主要是其形象,沾到哪里,哪里就是一片黄锈,非常难看,损害环境。其废涂应罐装好由专业的加工单位回收。对含三氯化铁废水的处理,最普遍的处理方法是投入石灰乳,它不仅能驿酸起中和作用,还对废水中的三价铁及其它金属离子有沉淀作用,并对废水中的杂质有凝聚作用。
除油的作用
除油的目的是除去金属表面的油垢,作为需要金属蚀刻的工作不管是加工线路板或是加工一般的机械零部件还是装饰性工件,也不管是加工航天航空部件或是舰船等高要求工件。在这些待加工的工件中,有些是要进行图文蚀刻,有些是要进行结构蚀刻,有些只对其工件的一面或双面进行整体化学蚀刻。对这些工件的表面首先都必须要进行有效的清洁处理。一个理想的清洁表面必须是除了油脂、防锈层、氧化皮,同时又洗去了各种标记符号和其他不溶性外来物质的表面。这一清洁作用的目的是为了保证防蚀层在金属表面的粘附力和蚀刻速率均匀一致所不可缺少的条件。
?
水洗的作用
水洗在金属蚀刻的整个工艺流程中是采用得做多的一个步骤,每经过一次处理其后都要进行水洗。水洗的目的:1.要洗掉从碱性或酸性溶液中取出的工件表面所附着的碱性或酸性液膜代之以清洁的水膜,从而成为清洁的表面;2.工件从一个工序转移到下一个工序时,不至于将上一个工序的溶液带到下一个工序的溶液中。所以,水洗在金属蚀刻的圈过程中是左右其产品质量的重要过程。
脱膜原理
?通过较高浓度的NaOH(1-4%),将其加温至将50℃左右,NaOH具有强腐蚀性,其与钢片表面的感光材料发生化学反应,将保护钢片表面的感光材料剥离。
蚀刻加工的厚度范围
蚀刻加工的材料厚度;0.02-2.0mm,最佳的蚀刻厚度:0.05-0.5mm.
金属蚀刻能达到的精度:当材料厚度为T=0.05时,可开最小的孔为:∮=0.1mm;蚀刻孔的直径∮与材料厚度T的关系:∮=1.2*T--1.5*T,薄的材料蚀刻的精度高,厚的材料蚀刻的精度低, 蚀刻的过程是化学反应变化过程,材料薄,化学反应的时间短,变化过程管控调整可控,材料厚,蚀刻时间长,变化过程不可控的成份多,精度就差。
不锈钢硬度对照表
不锈钢硬度换算, 供大家参考
金属蚀刻的工艺流程
开料→清洗板材→干膜或涂布→烘干→曝光→ 显影→烘干→蚀刻→脱膜→检测包装
蚀刻钢片的连接点设计
金属蚀刻连接点案例图
1、外凸试式
外凸试连接点设计主要是应用于标牌,手机外壳,产品的外壳等表面键,外观看上去不可有毛边、凹点等缺陷。外凸试计也有两种方式,一种是材料厚度大于0.3时,连接点可以设计为正面半刻,背面才有连接点,方便打磨等方式去掉;另一种是厚度小于0.3时,连接点不可半刻,以下图纸是第一种设计方案! 材料厚度在0.2 以下时, 可以做到无连接点,但需要经过2次蚀刻,导膜, 良率低, 成本会大大增加, 一般不建议用这种方式.
2、内凹试的连接点
内凹试连接点设计主要是应用于功能性产品,毛刺凹于产品的边缘,不影响产品的功能。材料的厚度不同连接点的大小也不同,材料越薄,金属蚀刻连接点越小,材料越厚,蚀刻连接点越大!厚度在0.2mm以下的,,内凹的宽度在0.5mm,内凹的深度在0.15mm内! 一般产品都会选择这种内凹的方式, 部分客户还会对连接点的大小有相关要求!
卓力达专注蚀刻加工、金属蚀刻、不锈钢蚀刻、五金蚀刻,是深圳专业的蚀刻加工商。卓力达电子有限公司为您贴心解决金属蚀刻工艺的各种问题。
联系人:隗(yu)小姐:0755-2708 8797 13620203959 yw6@zldsmt.com ; yuch@zldsmt.com
